Ancient low-temperature small tatara iron making
Iron sand from different production areas has characteristics such as being easy to reduce, being difficult to handle but using the base iron as an old sword, having a high carbon content but being soft, and having a pronounced skin and blade pattern function. I am researching ways to bring out my strengths every day.
Even with the same type of iron sand, depending on the type of tatara charcoal, the yield may be poor, or it may turn into pig iron, and the yield may be significantly reduced depending on the amount of iron sand added, so a small adjustment can greatly affect the result. So it's difficult.

Iron sand from all over Japan.
Although the color and grain size may vary slightly,
The ingredients and properties are more individual, and how they are combined or used alone will determine what kind of sword is being made. This is just an experience.
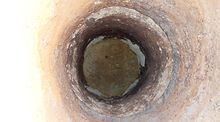
Inside of tatara equipment
The bottom part is hardened with clay. The diameter is approximately 40cm and the inner diameter is approximately 30cm.
It was made using a small drum.


Add charcoal and iron sand alternately. The difficult part is adjusting the air volume from the blower based on the firing power of the charcoal, the reducing power of the iron sand, the properties of the iron sand, etc., and deciding what kind of pigeon or iron to make.
The flame rising from the tatara device turns orange, indicating that reduction is occurring.
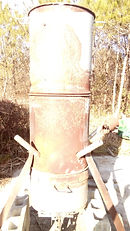
It has three tiers, and the bottom part is lifted and joined by jacking up a car, so it can be done by just one person when setting out. There are 4 ventilation ports and commercially available stainless steel piping is used. Connect the washing machine's drain hose to the blower and blow air through it.
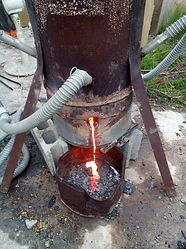
Remove slag once every 20 minutes.
The impurities contained in the iron sand (phosphorus, sulfur, manganese, etc.) in slag have a low melting point, so they separate from the iron sand and accumulate at the bottom. By removing them, oxygen and carbon stick together and become carbon dioxide. After being released, iron remains.

It is in a state of exfoliation.
You can see that keratin is generated on the bottom.

The tatara is taken out of the tatara equipment, placed in water to cool down quickly, and any slag etc. that clings to it is peeled off.
This time, we made 6.5 kg of iron sand and 8 bales of charcoal, so the return rate is about 26%.